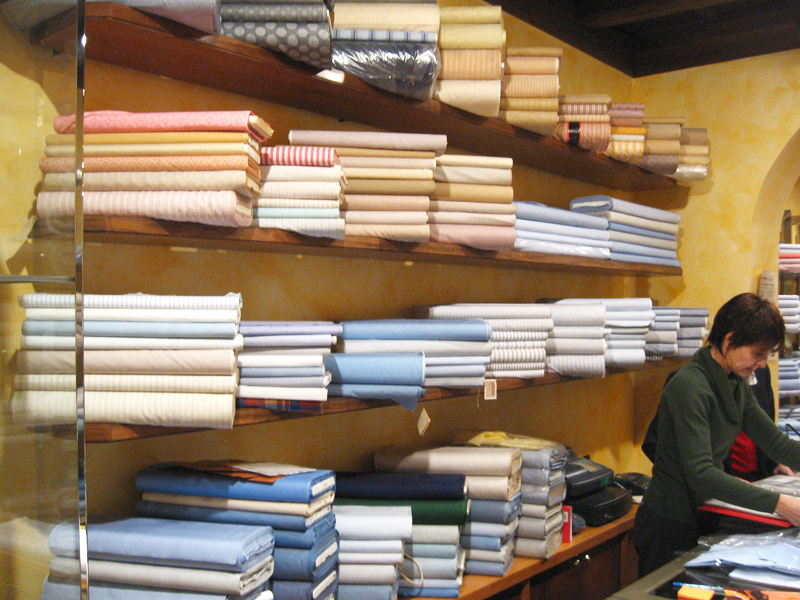
The number of options available through a custom shirtmaker can be both a pleasure and a pain. Any good shirtmaker, for example, will have hundreds, if not thousands, of shirt fabrics. If you haven’t given it much thought before going in, you can easily be overwhelmed by the options. To know which you should choose, it helps to know a little about shirtings (fabrics used for shirts). Here are some basic terms:
- Plys: Shirtings are usually made from raw cotton, which are spun into yarn and then woven into fabrics. Higher quality fabrics will be made from yarns that are twisted together, which is done to make them stronger. Imagine them like a braided rope. The more ropes you braid together, the stronger the final rope will be. Thus, a two-ply yarn means the fabric has been made with two yarns twisted together, and a single-ply means each yarn stands alone. Obviously, more plys the better, but shifty manufacturers often use two ply yarns going lengthwise (warp), and then one ply yarns going crosswise (weft), and they’ll still call the final shirting two ply. When you hear of a shirt being 2×2, however, you know that there are two-ply yarns going both ways.
- Yarn number: Shirtings can be made from finer or coarser yarns. As you go higher on the number scale, the yarns will be finer and thinner, which in turn will make the shirting will feel softer and silkier. The highest yarn numbers are downright heavenly. The trade-off, as you can guess, is that they’re less durable. The issue is actually not that different from “Super Wools” in suitings.
- Thread count: This isn’t advertised that often, but when it is, it refers to the number of yarns per inch. More densely woven materials will have higher numbers, and more openly woven materials will have lower ones.
Of course, there’s more to fabric than plys, yarn numbers, and thread counts. The real character is determined by how the yarns are woven together. These can be broadly classified in the following ways:
- Plain weave: Your most basic shirting is woven in a plain weave. That includes things such as poplins and broadcloths. Here, each lengthwise yarn passes over each crosswise yarn – over and under, over and under. The effect is something that’s very durable, resistant to shrinkage and wrinkling, and dimensionally stable. In other words, it’ll last a long time and probably serve you well as a basic business shirt.
- Basket weaves: A basket weave is like a plain weave, but one crosswise yarn passes over two lengthwise yarns. In this category are oxfords and pinpoints. The effect is something slightly more texturally rich, but the trade off is that it’s less durable. The “floating” yarn is more likely to catch or snag on a broken fingernail or splinter.
- Twills: Twills have a diagonal ribbing effect (like what you see on denim), and they include gabardines, cavalry, and herringbone. The upside to twill is that it’s the most durable of cloths and least likely to soil. The downside is that they’re the hardest to clean once they do.
- End-on-end: These are plain weaves, just like broadcloth, but they have an interspersion of colored yarns with differently colored yarns. The effect is a crosshatched appearance. Like basket weaves and twills, I favor these over basic plain weaves because they’re slightly more interesting and visually rich.
- Dobby and Jacquard: Both of these are just ways to achieve a design on a cloth without using different colors. Use them with caution, however, as you could end up getting a shirt that looks like it was made out of a couch fabric.
It’s worth noting that fabrics woven on old shuttle looms tend to be longer-lasting than ones woven on more modern machines. That’s because newer machines speed up the weaving process, and the faster you run the looms, the greater inherent tension there is in the yarns. On today’s super-high speed looms, the resulting yarns have many microscopic breaks all over them. As you wear and launder your shirt repeatedly, these breaks will worsen with time and your shirt will degrade more quickly. Thus, don’t go off of weaves and numbers alone. The quality of a cloth is heavily determined by which machines were used to make it as well.
Before you go into a custom shirt maker, think about the colors, designs, and functionalities you want. If you know you want a blue Bengal-striped shirt, for example, that will allow the shirtmaker to pull out some swatches for you to consider. You should also think about the weave you want. A densely woven broadcloth will be good for winter, when you need to retain heat. Oxfords, on the other hand, tend to have more open weaves, so they’re better for summer, when you need more breathable fabrics. Similarly, think about whether you want something with a smooth finish, like a plain weave poplin, or if you prefer end-on-ends and twills for slightly more textural interest. By considering these things before you to go the shirtmaker, you can more easily decide between fabrics when they’re placed in front of you.
Come back next week, when we’ll actually review some of the shirtmakers out there, and talk about the advantages and disadvantages of each.
(Pictured above: Francesca Romana and some fine shirtings at Mimmo Siviglia’s store in Rome. You can read about Mr. Siviglia in my article at A Suitable Wardrobe. Also, this article owes itself to a primer written by Alexander Kabbaz, one of the leading experts on custom shirtmaking)