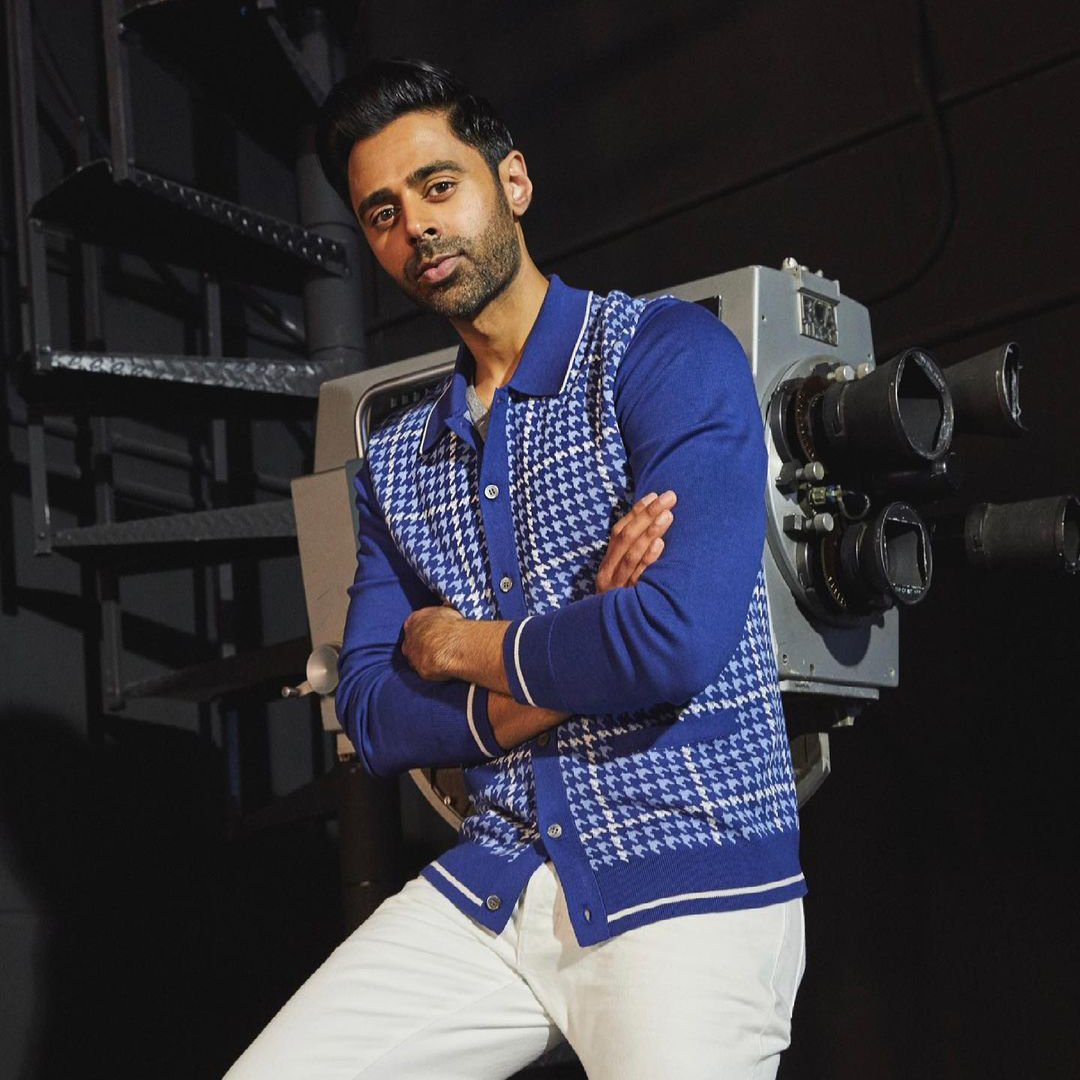
In Todd Snyder’s latest ad campaign, comedian Hasan Minhaj can be seen wearing an electric blue, houndstooth cardigan with white highlights. The sweater looks like it could have been custom-made, as the shoulder seams, chest, and hem all hit him at the right places. But in reality, when Minjaj walked into his photoshoot that day, this was likely the first time he tried the sweater on.
How is it possible for some designers to come up with clothes that fit so perfectly off-the-rack? The answer lies with a process that involves small teams of pattern makers, technicians, and fit models.
Fit models aren’t like other types of models. Instead of strutting down catwalks or gracing the pages of fashion magazines, fit models work behind the scenes during a garment’s production process. Their job is to professionally wear clothes, so that designers, pattern makers, and technicians can assess a garment’s fit and performance. In some ways, they’re like living mannequins.
To understand how this process works, we have to review how clothes are made. Every idea starts with a sketch in a designer’s notebook. A designer will sketch out the general idea that they’re thinking about for a shirt, jacket, or pair of pants, which will inform their design choices for fabrics, trims, and general silhouette. Next, a designer will work with a pattern maker to create a pattern, which is the industry’s term for a garment’s architectural blueprint. A pattern is how someone on the factory floor knows how to cut each panel, which in turn determines the garment’s shape once it’s sewn. It’s only after a pattern is developed that a sample garment can be constructed.
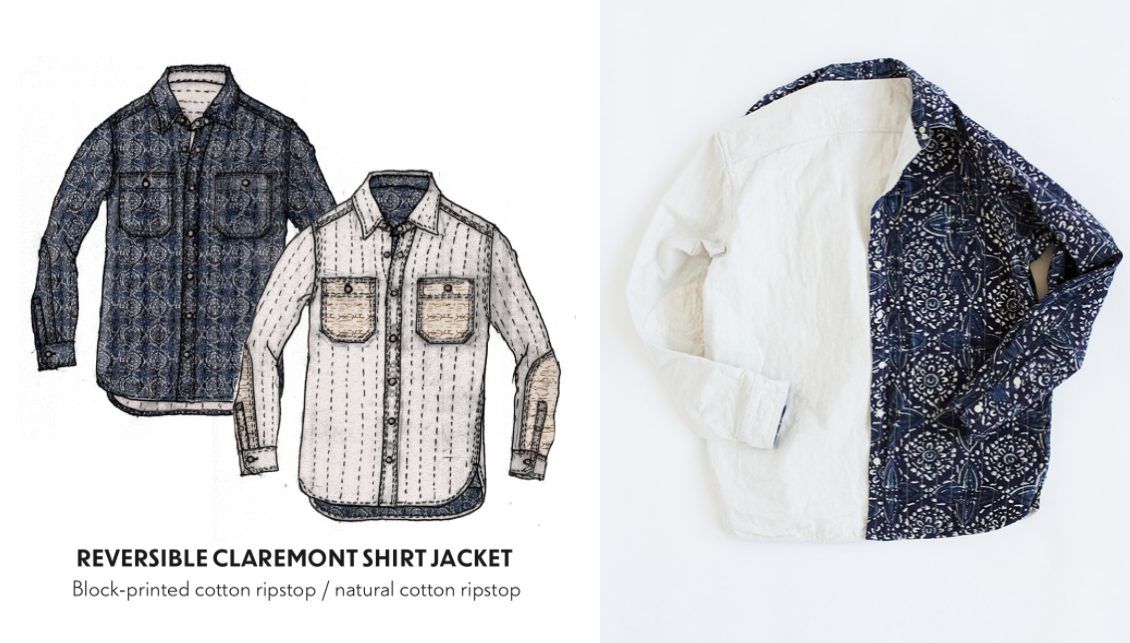
On the left, a sketch of an 18 East reversible shirt jacket. On the right, the final garment
Once a sample garment has been made, it’s put onto a fit model, typically someone who fits the industry’s profile of a men’s medium (i.e., someone with a 40″ chest and 32″ waist). From here, the pattern is refined, depending on how the garment fits, and another sample is produced. This step is crucial for brands trying to improve their sell-through rates and avoid returns.
The New York label 18 East, known for its unique designs, beautiful fabrics, and oversized silhouettes, had challenges when it launched in 2018. “The way the product is styled on our site is how we intend things to fit,” designer Antonio Ciongoli explained on Styleforum. Initially, Ciongoli sized and cut his patterns to fit as they do in their brand’s product photos. But when he started receiving feedback and questions regarding sizing, he began working with a fit model. “We developed our fits with an industry-standard fit model to ensure that a medium fits like how most people think a medium should fit. That, frankly, is not how I think a medium should fit, but it has changed returns on us dramatically.”
A fit model’s experience can make a dramatic impact on how the pattern is adjusted. Beginner fit models may not do much more than stand still when a garment is being examined. But those with more technical experience and stronger brand relationships can provide more meaningful feedback. “Someone new to the business may not fully understand how a pattern is drafted or how a garment is made,” says John Gallagher, founder of The Critical Fit. “At best, they may only be able to describe how they feel in the garment. I can confidently say this because that was me when I started.”
Twenty-five years ago, Gallagher was a model looking to diversify his portfolio. A friend introduced him to a brand looking for a young men’s medium, and he found that his body happened to match the industry’s standards for such fits and proportions.
Today, Gallagher is one of the industry’s leading fit models. Over the years, he’s partnered with brands such as Todd Snyder, Ralph Lauren, and Brooks Brothers, helping them refine their fits and silhouettes. Gallagher says he starts every fitting by looking at the designer’s intent. “What does the designer want for this style? Who is it for? How do we want the customer to feel in these clothes?” he asks. “When I’m evaluating a garment, I’m like that diagnostic computer that you plug into your car to find out if something is wrong and, just as important, how to fix it. When I find something isn’t quite right, I’ll make suggestions on how to address the problem.”
Feedback isn’t always as simple as saying whether something needs to be slimmer or larger, or if the fabric is uncomfortable. “It’s important to understand how making changes to one part of the garment may impact another part negatively. During a fitting, I’m looking at every possible reason why a customer might not want to buy it. This includes the fabric, feel, wash, button placements, stitching tension, and thread size. The list is as long as you can imagine, especially with all of the different product categories. A fit model also has to know how to communicate these issues to technical teams.”
Sometimes Gallagher’s work follows him home — literally. “If I see something during a fitting, I may take the garment home and wear it for a day or two. I may also wash and measure it, and then create a report with photographs of the ‘before and after.'” These tests are done to make sure the fabric doesn’t stretch out with washing and wearing, which would affect the fit and silhouette. Given the production volume at some brands, such careful testing and evaluation can save a company millions of dollars.
Gallagher’s reputation as a fit model is so strong that, in 2005, he partnered with Alvanon, an apparel product development company, to make a mannequin based on his measurements. These mannequins are used everywhere, from the design process to the factory floor. Companies can purchase generic forms based on industry specs, but most prefer Gallagher’s humanized version. “They want to make sure that it’s the guy as opposed to a guy or generic version,” says Gallagher. Gallagher even has a virtual avatar of himself that companies can use during the pattern development phase to see how a sample will fit.
Fit models also come in different sizes. After a company nails its first sample garment, the base pattern is graded up and down for the other sizes. In this way, a mens’ 40 is turned into the 36, 38, 42, and 44. Some companies will then opt for another round of fittings with different models in those sizes. This commonly happens for top-selling garments or something with a lot of inventory, but this isn’t always an option. When it’s not, it’s again up to the original fit model’s experience.
“From a grading perspective, you get a feel for it, what works in each product category for all sizes. Just because I’m a medium, it doesn’t mean that I’m not thinking about what my size is going to grade to for an extra-large.” However, certain areas require their own fit models, such as the Big & Tall section, which grades on its own unique scale.
So the next time you buy something and love the way it fits and feels, don’t just thank the brand and designer, but also remember that a small group of fit models were probably responsible for everything in your closet.
Gallagher has a few tips for making sure your clothes fit well when trying them on:
- For pants, Gallagher suggests knowing your size and watching out for critical details. This includes seeing if the waist is too big, the hip is too shapely, or if the saddle is too narrow. “What you want in a pair of pants is to have a nice, neutral stance and an easy stride when you walk. If there’s any restriction there, you might want to either evaluate a different size, and if that doesn’t work, perhaps it’s the shape that is creating the issue.”
- For jackets and shirts, “it’s all about the neck, the shoulder slope, and the armhole. You want to have a nice lateral lift and forward reach without feeling it.”
- If nothing else, Gallagher encourages you to trust your instincts. “People know what they don’t want, that’s for sure.”